Sandvik Presents Steel Belt-Based Conveying For Enhanced Hygiene At Interpack
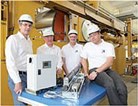
Sandvik Process Systems will focus on the cleanliness and hygienic qualities of its endless stainless steel conveying and processing belts, launching a compact, self-contained conveyor system that opens up the benefits of this technology to new markets.
Steel belts are widely used in drying, cooling, freezing and baking applications, and its inherent cleanliness – the flat, smooth surface of a steel belt is easy to clean and impervious to bacteria and odours – makes it ideal for all kinds of conveying operations.
One area where concerns over hygiene have put food safety and sanitation at the top of the list of priorities is meat processing and Sandvik will highlight research showing a significant reduction in the risk of bacterial build-up when using steel belt technology.
Research by Finnish food laboratory VTT Expert Services Ltd has shown that stainless steel belts are more cleanable than plastic conveyor belts, and that this benefit is even more marked as belts become worn or damaged.
The research measured residues left after cleaning a Sandvik stainless steel belt and two types of plastic conveyor – solid and laminated – with tests carried out on new and ‘damaged' surfaces. The results clearly demonstrated the enhanced cleanability of the stainless steel surface.
"The smooth, hard surface of the steel belt has two key benefits," explains Håkan Eriksson, manager of application technology at Sandvik Process Systems.
"Firstly, there are no holes, textures or fibres in which bacteria can hide and grow. Secondly, the belt is easy to clean by whatever method is most appropriate: heat, pressure, brushes, detergents, chemicals or a combination of these."
Compact, modular conveyor system
Sandvik, who this year mark 110 years in steel belt production, will introduce a compact, steel belt-based conveyor system designed for meat processing and other hygiene-critical applications.
A modular framework offers a choice of lengths from 2.5-15 m, and belts can be supplied in widths from 600-1500 mm. Open on one side, the unit allows quick installation of endless belts, eliminating welding and ensuring maximum hygiene. Other key features include easy adjustment of tension and parallelism, efficient drum motors and a framework that delivers high strength and stability from a lightweight design.
"The benefits of steel belt-based conveying are well established and widely recognised" explains Eriksson. "What this unit brings to the market is the ability to apply these benefits to applications where steel belts might not previously have been considered.
"Its compactness is a major breakthrough, as is the flexibility of configuration made possible by its modular design."
Sandvik produces a range of steel belt-based processing systems with applications relevant to Interpack visitors. Its Rotoform® granulation system provides a efficient method of solidifying molten products (e.g. cheese, chocolate, emulsifiers, fats, chewing gum base) in an easy-to-handle and store pastille form. The company also supplies casting systems based on highly polished steel belts for producing packaging foils and films.
SOURCE: Sandvik