Lower Costs & Productivity Boost For Poultry Processor
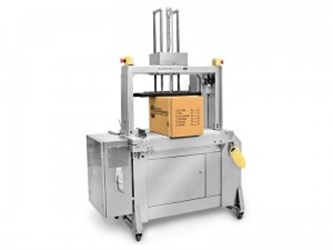
In the post-recession investment void of 2009, strapping system supplier EAM-Mosca made the decision to aggressively enter the animal protein market with a novel product concept. In an industry where many companies historically purchased lower priced banding equipment, Mosca decided to offer a high performance solution that would provide superior reliability and lower operating costs. The biggest impact on processors, however, would be the ability to move to greener, lighter, lower-cost consumable products to provide lowest total cost of ownership, although at a higher initial cost.
The first trials in 2010 were learning experiences as EAM-Mosca sought to fully understand the harsh environment of the plants, while training personnel in new technology. The industry’s demanding application requirements challenged the EAM-Mosca technical and sales team which led to system refinements.
By late 2010, the first major installations were running smoothly. By 2011, they had proven their claims of improved productivity and low cost of ownership in multiple locations.
A published story summarizing success at a major poultry processor came to the attention of another poultry plant in East Tennessee. In early 2012, plant representatives tasked the EAM-Mosca team with demonstrating to them the benefits of the Mosca system.
The trial began with installation of a Mosca model TRP-5-STS fully automatic, high-speed, stainless steel strapping machine with proprietary Sonixs ultrasonic sealing technology. The machine was set to run with lower-cost 6mm Polypropylene strap, downsizing from the traditional 9mm that the plant had been using.
By virtue of the superior weld strength of the Sonixs technology, the lighter strap was quickly approved for the operation’s 10k and 15k boxes of processed chicken. There was the typical learning curve with operators and maintenance personnel, but the commitment of both customer and supplier to the success of the trial helped to work through early issues. The trial was ultimately judged a success and led to an order for two strapping machines during summer of 2012.
After a little over a year, the EAM-Mosca team returned to assess the success of the installation. The two Mosca banding machines have each clocked well over two million cycles and are performing reliably as promised. The plant’s conversion to 6mm strap has gone smoothly, with no reduction in package integrity. In fact, the Mosca double press, a feature not included in the prior equipment, provided the added benefit of uniformly compressing and flattening the product carton lids prior to strapping and more importantly, after the post-strapping freezing process. Flatter boxes mean more stable pallet loads and improved shipping security, as well as increased customer perception of quality. In addition, the conversion to 6mm strapping provided the processor significant cost savings and more. First year savings totaled 27.5% or about $57,000. Meanwhile, more footage on a coil of strapping reduced coil changes by about a third, positively impacting packing line productivity.
Further savings were achieved in replacement part costs. The prior generation of strapping systems in the plant required $16,000 in parts in 2011. By comparison, the Mosca system’s first year, the valued of replacement parts was only $2,800. The processor actually paid less than this amount due to Mosca warranties, but the actual usage savings was 82%, or another $13,200.
There are most certainly additional savings from higher throughput and lower downtime as well as reduced maintenance labor costs, but these numbers are not available for publication. In total, with an equipment investment of approximately $72,000, this processor acknowledges savings totaling over $70,000, not counting productivity benefits.
To any manufacturer, a one year payback is a successful investment. To this poultry processor, the success of the project was further acknowledged by their purchase of a third Mosca strapping machine model TRP-5-STS in late 2013. In addition, there is talk in the plant of reducing the number of packing lines due to improved throughput. As conditions in the poultry market have improved in the last year or two, the fiscal outlook in this plant has improved even more based on the lower cost and higher productivity of its strapping operation.
To the EAM-Mosca team, this particular system installation and projects like it, confirm the value of its performance-based approach for this competitive market segment. EAM-Mosca is confident they can assist other plants to achieve similar cost and productivity improvements.
EAM-Mosca Corporation provides high-performance strapping system solutions to a variety of industries, including pharmaceutical, warehousing, corrugated, food, graphic arts, mailing, fulfillment, logistics, wood, and other industrial or consumer goods. The company combines innovative equipment with strapping materials manufactured to maximize machine performance, and customer support programs that help customers meet their performance and productivity goals.
Source: EAM-Mosca